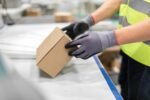
Visit Our Sponsors |
|
|
|
|
|
|
|
|
|
|
|
|
|
|
|
|
|
|
|
|
|
|
|
|
|
|
|
|
|
|
|
|
|
|
|
|
|
|
|
|
|
|
|
|
|
|
|
|
|
Toys. Pet food. Toothpaste. You can't open a newspaper these days without reading an article about yet another high-stakes product recall. Many of the high-profile stories this year have related to products produced by contract manufacturers (CMs) in China or India. Clearly, controlling the quality of outsourced goods is critical. Reputations built over decades can be destroyed overnight, especially when emotional issues, such as lead-paint-infested toys, are involved.
But damage to brand image is not the only harm that arises from poor quality. Quality-related expenses, such as warranty claims, supplier chargebacks, and disposal costs, can take a huge bite out of manufacturers' bottom lines, something that most can ill afford given the pressures of globalization and other economic realities. Many companies that outsource production in pursuit of lower costs quickly find that the ultimate price of entrusting a third party with their brand is very high indeed.
"Managing supplier quality and in-process quality--those are huge challenges for manufacturers in a CM environment," says Simon Jacobson, senior research analyst for AMR Research. "Autonomous facilities resist having to march in the same line, so getting composite metrics across plants is elusive."
Source: Managing Automation, http://managingautomation.com
RELATED CONTENT
RELATED VIDEOS
Timely, incisive articles delivered directly to your inbox.