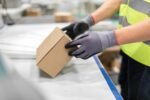
The concept of everyone in a choir singing from the same page of the hymnal has deep historic and cultural roots. But for those working in manufacturing, achieving this vision has been a struggle.
People in product design, engineering, procurement, assembly, testing and servicing are each focused on the specific types of data related to their own tasks and department responsibilities. And they maintain their records accordingly.
Information that’s appropriate for one phase of a product’s lifecycle might not appear to have much relevance for the others. Even when it does, those connections might not be readily apparent. For example, units of measurement for data housed in separate silos might not translate well. Goods in production often move from stage to stage cloaked in a thin and nearly threadbare veil of information.
Here’s where the idea of a digital thread comes in. Initially spearheaded by the military aircraft industry out of a desire to improve the performance of future programs, the digital thread has emerged to become the technical foundation of Industry 4.0 and smart manufacturing. It’s part of a growing movement to break down data silos and better orchestrate a product’s digital twin representation, providing a virtual and physical product with perfectly matching characteristics that can be shared across the entire supply chain.
The Linchpin of Digital Continuity
The digital thread provides a single source of the truth for an entire organization, enabling greater consistency, collaboration and alignment across functions. The term refers specifically to the communication framework that enables the flow of data throughout each phase of a product’s lifecycle. It supports continuity of operations across products, processes and people. But getting there isn’t easy.
As you might expect, building a digital thread requires investing in systems and digital technology, along with a culture shift toward greater openness and sharing of information. The latter is typically the bigger undertaking. With many companies, it will involve changes to traditional operating departments and the dismantling of data silos. Once aggregated, the data can be analyzed to align with innovation and the “greater good” of meeting market demand and exceeding customer expectations. Along the way, it can be used to streamline product design, increase product quality, build closer relationships with customers and suppliers, and increase profits.
For a full digital transformation as part of an Industry 4.0 strategy, a digital thread needs to be embraced across the organization. This is the only way such an initiative can be fully effective. Data needs to be shared with groups of individuals and departments, each with an interest in maintaining it. For most organizations, that involves a cultural change in which many peoples’ cheeses get moved, frequently engendering resistance.
Maintaining the Digital Twin
Much has been written about the digital twin, less so about how to maintain a virtual representation of a product. 3-D models of physical products are quickly becoming the basis for engineering collaboration, quality assurance and testing, manufacturing, and sustainment services following delivery to the customer. Further, troubleshooting issues can be handled by experts from remote locations using the product’s digital representation, rather than their having to travel to see and diagnose the product itself. But if a digital twin isn’t accurate, none of these benefits can be captured — at least not for long. Here’s where the digital thread comes into the picture: by providing the necessary digital continuity to ensure that the virtual product is updated in perfect synch with what changes with the physical product.
Beyond these synchronization challenges, other cultural issues remain to be resolved. For example, can vendors see past their desire to use their own product formats to hold on to a segment of the market? Are they comfortable participating in open data exchange standards that facilitate multi-vendor participation in the digital thread? Do the makers of materials, components, and software have the bandwidth to move ahead when they already feel overwhelmed meeting the short-term improvement goals they’ve promised? No one knows for sure. Transformation is unsettling, uncertain, and hard to do. And democratizing data isn’t always a comfortable fit for hierarchical organizations.
Even so, a number of leading manufacturing companies have made the commitment to building and leveraging digital threads.
- Volvo Group is using the concept it to accommodate custom motor configurations. Its digital thread streamlines engine quality control and assurance processes, and integrates information across multiple software systems.
- The Carlsberg Group brewing company is optimizing its manufacturing processes with a digital thread across its production sites, floors and machinery, to tap into information within its critical manufacturing systems. As a result, Carlsberg can use digital twins to access key performance indicators at the global, factory, and even production-line level in its 100 brewing sites.
- Mercedes-Benz is applying the digital thread to enlighten its customers. A mobile application using augmented reality digitally overlays engineering information onto the vehicle’s dashboard to educate drivers about the vehicle’s features.
The digital thread, with its emphasis on digitized records, 3-D models, and digital twins, represents a powerful way forward for manufacturing organizations, particularly those in the defense industry. But the full realization of a digital enterprise can only be achieved where there’s a willing and responsible collective ownership of the organization’s digital thread.
Tom Hennessey is chief marketing officer of iBASEt.