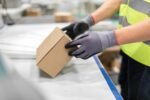
Visit Our Sponsors |
|
|
|
|
|
|
|
|
|
|
|
|
|
|
|
|
|
|
|
|
|
|
|
|
|
|
|
|
|
|
|
|
|
|
|
|
|
|
|
|
|
|
|
|
|
|
|
|
|
In today's tight economy, retailers are striving to cut costs in any way they can, and one popular method is to carry less inventory throughout the supply chain. Still, as we move into 2010, retailers want the best of both worlds, so they also want to be able to optimize the triggering of replenishments in order to keep the shelves stocked.
The challenge for retailers and manufacturers alike is that capacity, time and cost are the holy trinity of managing their supply chains. They have to ask themselves: How long is it going to take me to get product to market, how much is it going to cost me, and do I have the equipment to do it?
The ability to maneuver inventory through the network, through processes such as cross-docking and flow-through, is better enabled when a retailer or manufacturer understands the demand signals from the shelf and the transportation constraints within the supply chain. That's where transportation management systems (TMS) comes into play.
TMS is the glue that moves the inventory between all the nodes - the plant, the distribution centers, the warehouses, and the stores. It manages that cost, capacity, and time of moving inventory. This helps retailers to optimize the sell-through while lowering safety stock or the overall amount of inventory it has to keep on hand at each node in the supply chain.
This becomes more and more difficult as retailers start to grow. They have to deal with more SKUs, more stores, more volume, more international suppliers, more trailer capacity. And the more all of that grows, the more challenging it becomes to scale and still manage those constraints without assistance.
When retailers want to ship something, they attempt to predict the precise amount they will need. Some use flowcasting to figure out the time-phased replenishments so they can keep the shelves stocked in a timely manner. For instance, if the flowcasting tool identifies an anticipated stock shortfall two days from now, the demand signals can be sent up the supply chain to ensure the replenishment arrives before the stockout occurs.
Whatever that replenishment plan is, a well-designed TMS should be able to optimize the cost and movement of those goods through the supply chain all the way to the store shelf. This enables the retailer to optimize its sell-through because it can do a better job of predicting how much it needs based on where it is going, and there is less of a need for buffer stock to cover the variables that the TMS knows about.
Managing capacity, time and cost remains the biggest challenge in today's supply chain. Retailers, manufacturers and suppliers who can optimize their ability to manage those areas through the use of demand signals and TMS will have a significant competitive advantage in 2010.
Source: RedPrairie
RELATED CONTENT
RELATED VIDEOS
Timely, incisive articles delivered directly to your inbox.